Fully Adhered or Mechanically Attached: Which to choose?
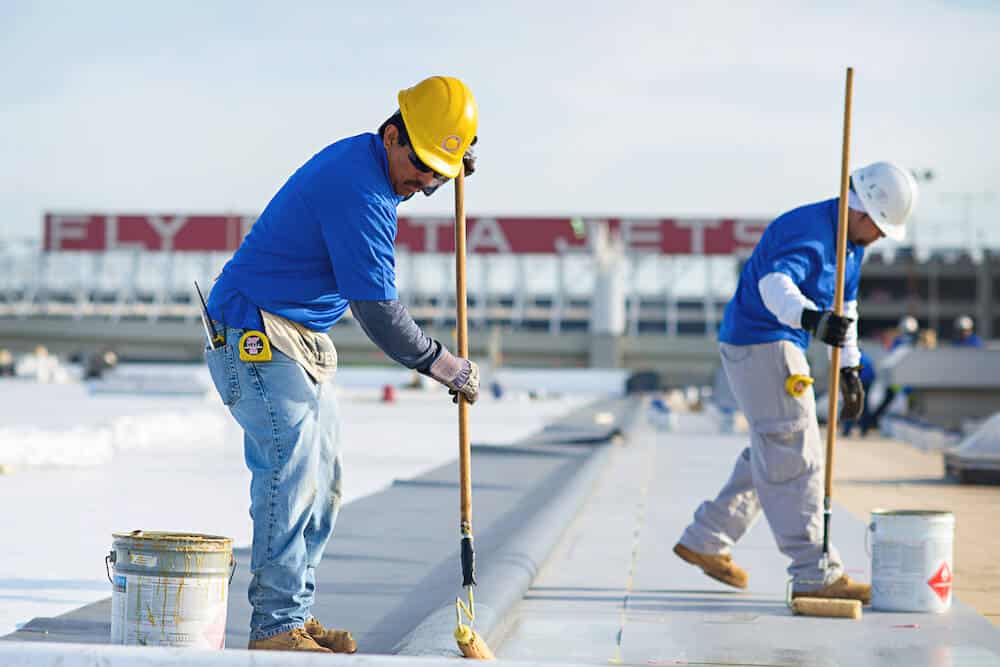
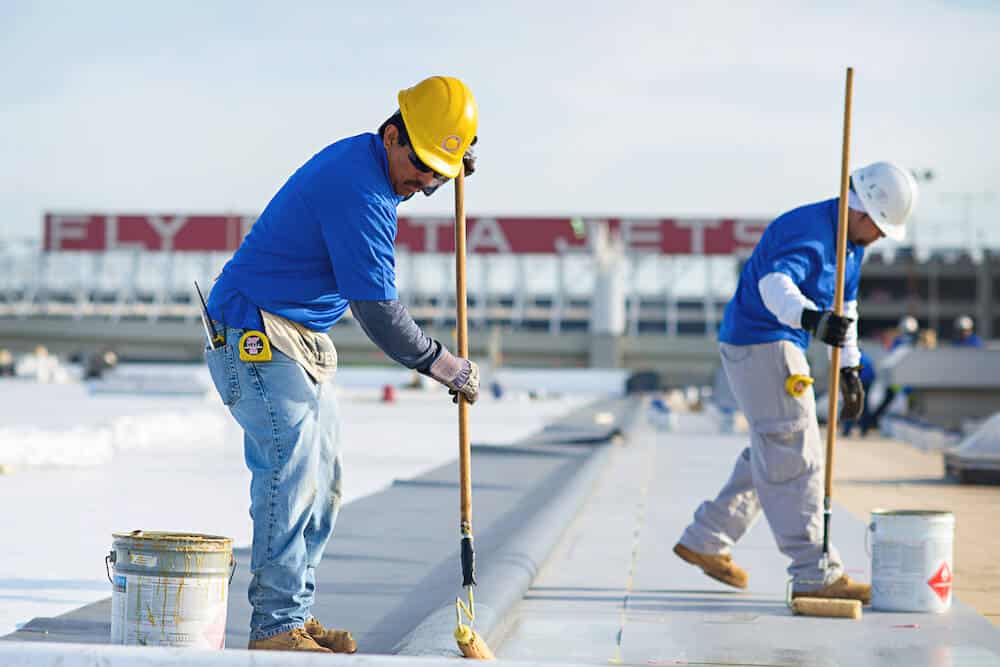
Roofs are typically fastened to commercial buildings in one of two ways: mechanically attached or fully adhered (there are others but these are the most popular). Virtually all roofs—fastened through either method—sit on top of a layer of insulation that rests between the roof and a metal deck, which is fixed to the structure below. Why do you care? Because failing to match your roof’s construction with your actual needs can mean you’re paying for value you don’t actually need.
Mechanically Attached
Mechanically attached roofs are by far the most common, dominating around 80% of the market. They can be installed faster and at a lower cost. Builders like them because they can be easily inspected by the manufacturer, who can quickly validate the workmanship by verifying the fastener pattern and their proper installation.
On top of most buildings is a metal deck, then a layer of insulation, then the roof. When installing mechanically attached roofs, the membrane roll is laid down and then the screws are driven directly through the insulation boards into the metal deck below. Typically, the screws are drilled in at the edge of the membrane roll then covered with the edge of the next sheet as the rolls are successively put down. A watertight seal is then created by heat-welding the membranes together with a hot-air gun. This seals any gaps and creates a single, flat, waterproof surface.
Fully Adhered
Roofs that are fully adhered are glued directly to the insulation below. This requires the 4’x8′ insulation boards to serve the dual role of insulating and securing the roof to the metal deck, which requires far more screws. This method is more expensive, slower, and can lead to additional challenges because large quantities of glue have to be applied at exactly the right time and temperature—but only after it has dried sufficiently to achieve the right level of tackiness. A weighted roller is then used to press the membrane onto the glue on the insulation below.
Builders choose fully adhered roofs largely because of the perception that they’re more resistant to leaks. The theory is that if you get a hole in the roof, the water can’t travel under the roof membrane past the layer of glue. But in reality, the odds are high that you won’t even realize there is a hole until enough water has pooled underneath to degrade the glue that adheres to the insulation below.
If this happens, you’re in bigger trouble than if you had a leak that you knew about right away. Hidden water that accumulates unseen beneath the surface can spread, resulting in greater damage to a larger area.
Fully adhered roof attachments can also provide higher Factory Mutual (FM) wind-uplift ratings. Factory Mutual is a large insurance company that has established the standards for commercial buildings, even for buildings that don’t use their insurance. While it’s true that fully adhered roofs have a higher FM wind uplift rating, it shouldn’t be the priority in much of the U.S. outside of coastal or high-wind areas.
Mechanically adhered roofs dominate the market for a reason—but fully adhered roofs are still popular for buildings in certain locations with specific needs. Talk to your roofer to determine what is right for your building based on these criteria.
LIKE WHAT YOU JUST READ?
Sign up for our newsletter to get fresh articles, updates and more!
Assess, Report and Decide: Get to Know Your New Building’s Roof
If you’re considering buying a new building, the very first item on your list should be to get an assessment of the roof’s condition. This analysis can prevent surprises down the line and—if the roof needs work—it can have a dramatic effect on the price you wind up paying for the building.
Why You Need A Roofer Onsite When You Install Your HVAC System
It’s common to place the heating, ventilating and air conditioning (HVAC) systems for large buildings on the roof. A successful rooftop HVAC installation usually involves the collaboration of an entire team of workers, so that issues related to the roof, structures, electrical and HVAC can be discussed beforehand. If an HVAC system is not coordinated…